Deep-Frying Waste in Fatty Acids to Rethink Plastics
The “FatLoop” project, based at the Max Planck Institute of Colloids and Interfaces and the Center for the Transformation of Chemistry, will use fatty acids from discarded oils to repurpose plastic waste into functional materials. Led by Dr. Manuel Häußler, FatLoop aims to lay the groundwork for a future beyond conventional plastics, with the long-term goal of developing fully recyclable and sustainable materials that match the versatility of plastics without their environmental footprint. The project has received €2 million in funding from the German Federal Ministry of Education and Research.
TAKEAWAYS:
- Key Innovation:The use of fatty acids from common cooking oils to fine-tune the molecular structure of plastic waste and achieve desired functionalities
- Applications: Upcycling polyethylene (PE) into 3D-printable filaments for in-lab equipment and porous filters designed for lithium extraction from deepwater sources in Europe
- Long-Term Vision: A technological platform and prototypes for sustainable and fully recyclable materials, using fatty acids to mimic the molecular structures of conventional plastics
Plastic waste is everywhere and poorly recycled—according to the latest UN figures, we produce 400 million tons of plastic annually worldwide, and only recycle 10%. From oil and gas extraction to refining, processing, and disposal, plastic contributes significantly to global CO₂ emissions.
The “FatLoop” research project tackles both existing plastic waste and the need for sustainable alternatives. Group leader Dr. Manuel Häußler’s innovative idea for upcycling is to deep-fry waste in oils to add extra functionalities. And using the same compounds derived from discarded oils (the "fat" in the project name), his team aims to create fully recyclable materials that could one day replace conventional plastics. “FatLoop” is based at the Max Planck Institute of Colloids and Interfaces and the Center for the Transformation of Chemistry, with €2 million in funding from the German Federal Ministry of Education and Research.
Häußler’s group will combine fundamental chemical research with technology transfer, supporting the EU’s goal of transitioning to an economy with a net-zero greenhouse gas economy by 2050. With the clock inexorably ticking, the “FatLoop” team proposes a recipe for a circular economy—the inspiration behind the "loop" in the project’s name. “We want to rethink waste as a resource for innovative chemistry, and create future-proof materials with properties comparable to conventional plastics minus its flaws—carbon footprint, resource depletion and pollution.” Häußler explains. “We’ll manipulate chemical structures in the lab, and make this knowledge available to industrial partners for a tangible impact.”
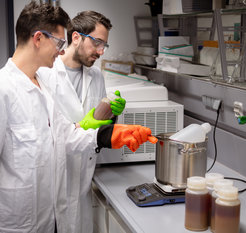
The team’s first target is polyethylene (PE) waste—the most widely used plastic, accounting for one-third of global production. Look around and you’ll likely see PE: in shopping bags, food and toiletries containers, cable insulation, and medical devices. But the same features that make PE so versatile—durability, lightweight, and resistance to degradation—also make closed-loop recycling difficult and energy-intensive.
Häußler’s team addresses this challenge by using fatty acids sourced from cooking oils that share molecular similarities with PE and can interact with and modify its molecular structure. The process begins in the lab, where single-use items like solvent bottles will be ‘deep-fried’ in fatty acids to produce 3D-printable materials. Imagine a thin, plastic-like sausage that can be reshaped into new equipment, triggering a virtuous circle where PE never leaves the lab.
The process can be adapted to various types of PE waste, as Häußler and colleagues discovered during an experiment that took an unexpected turn. When they set out to functionalize PE waste with fatty acids, they found that 'deep frying' also induces nanopore formation. These are ideal features for filtration materials, and “FatLoop” is planning PE-based sponges to harvest lithium from deep water. Lithium, a rare yet essential metal for batteries, is abundant in deeper rock layers but in highly diluted form. The porous filters would separate lithium from other components, like salts, ultimately reducing Europe’s reliance on imports and the environmental impact of traditional mining. “This application exemplifies the concept of upcycling we strive for: giving waste a second life, adding value in the process. It’s like recycling with a twist, to transform used materials into something new and more functional,” elucidates researcher Nico Friese.
Looking ahead, Häußler’s team envisions a future beyond conventional plastics, centered on fully recyclable materials derived from sustainable sources. The team will integrate experiments with systematic data analysis to better understand and tweak the molecular structures of circular materials made using fatty acids as key building blocks. These can be tailored to mimic the versatility of plastics while including chemical groups that enhance recyclability.
“It’s like embedding a recycling tag directly into the molecules,” Häußler notes. “FatLoop” will transfer lab-based insight to practical, scalable prototypes by working closely with the industry. “Our ambition is to break away from the cradle-to-grave lifecycle of conventional plastics. With fatty acids, we can design materials for reuse and repurposing from the start, with built-in recyclability” he emphasizes, aligning his project with the agenda of the UN Environment Program.
Center for the Transformation of Chemistry